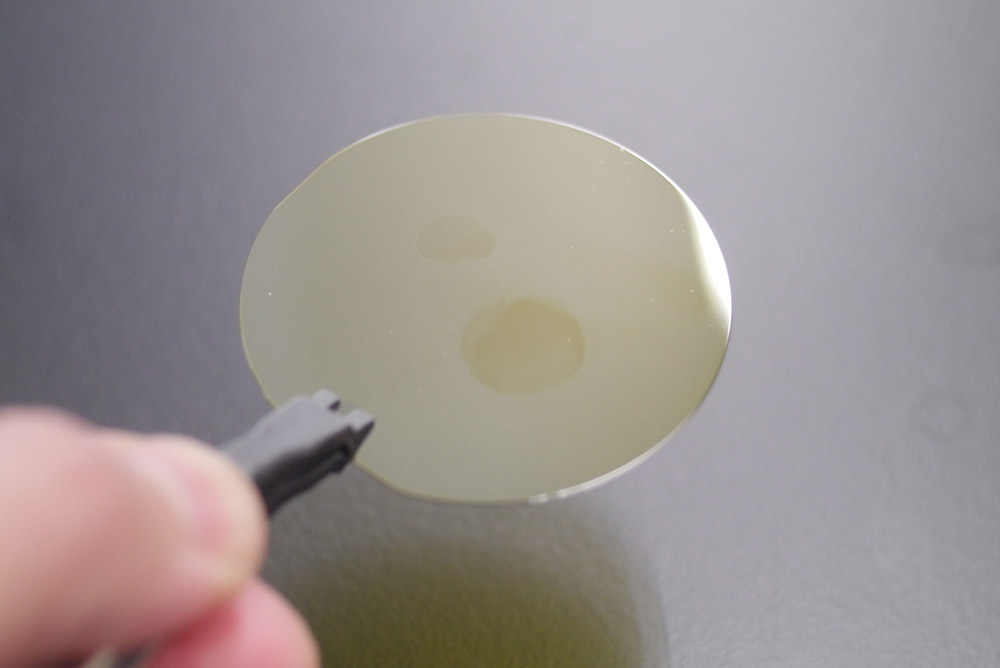
IoTやEV(電気自動車)の普及促進によって「パワー半導体」の需要が増加する中、新たな素材を用いた“次世代”パワー半導体の開発競争も激化している。ではなぜ、EVや電子機器においてパワー半導体が重要なのだろうか。立命館大学理工学部の村田順二准教授に、パワー半導体の最先端について聞いた。
●パワー半導体とは?
● 次世代材料のSiCや GaNがカギを握る
● 独自技術の開発で硬いSiCを研磨
● 加工時間の短縮が大きなインパクトを生む
● 基板の大口径化が今後の課題に
「パワー半導体」=「電力を制御する半導体」
半導体不足が世界的な問題になったが、そもそも「半導体とは何か」を理解している人は多くない。まして「パワー半導体」となると、さらに認知度は低い。まずは、パワー半導体の基本的な理解から始めよう。
「半導体は、条件を変化させることで『電気を通す/通さない』を制御できる物質のことです。スマホやパソコンなどのIT機器をはじめ、私たちの身の回りにある多くのものに使用されており、半導体なしに現代社会はなり立たないといってもいいでしょう。
そして、『パワー半導体』は、電力を制御する半導体です。たとえば、直流を交流に変えたり、周波数を変換したり、電圧を調整するといった用途で使われています。
次世代モビリティとして注目を集めるEVやハイブリッドカーのように、モーターを使って走る自動車や電車などは、パワー半導体なしには成立しません。電気自動車の場合は、バッテリーとモーターの間にPCU(Power Control Unit)という部品が入っていて、その中にパワー半導体が使われています。EVの普及に伴い、パワー半導体の需要は確実に増えるはずです。
パワー半導体は、自動車や電車といった極めて高い安全性が前提となる用途に使われるため、求められる耐久性や信頼性も非常に高くなります」(村田准教授、以下同じ)
次世代パワー半導体に使われる新材料とは?
現在、パワー半導体の最先端では、材料の高品質化や加工プロセスの高度化が進められている。その「次世代パワー半導体」のカギとなるのが、炭化ケイ素(SiC)や窒化ガリウム(GaN)などの新しい素材の活用だ。
「SiCやGaNは、『ワイドギャップ半導体』と呼ばれるパワー半導体の材料です。従来のシリコンを使った半導体よりも高い電圧をかけたり、電力のロスを少なくしたりすることができます。
また、もうひとつの特長は小型化できるということです。熱伝導率が高く、熱を発散しやすい性質を持っているため、冷却機構を簡素化することが可能で、ユニット全体のコンパクト化につながります。EVにおいては軽量化が極めて重要なので、SiCを使った次世代パワー半導体への期待も大きいのです。
また最近では、スマートフォンやノートパソコンなどの充電に使うACアダプターに、GaNを使ったワイドギャップ半導体の搭載が進められています。ワイドギャップ半導体の利用で、ACアダプターを従来の半分程度に小型化することができ、既に商用化されています。
次世代パワー半導体の材料は、極めて加工が難しい!
優れた機能を持つSiCやGaNを使ったワイドギャップ半導体だが、その開発は簡単ではない。それはなぜか?
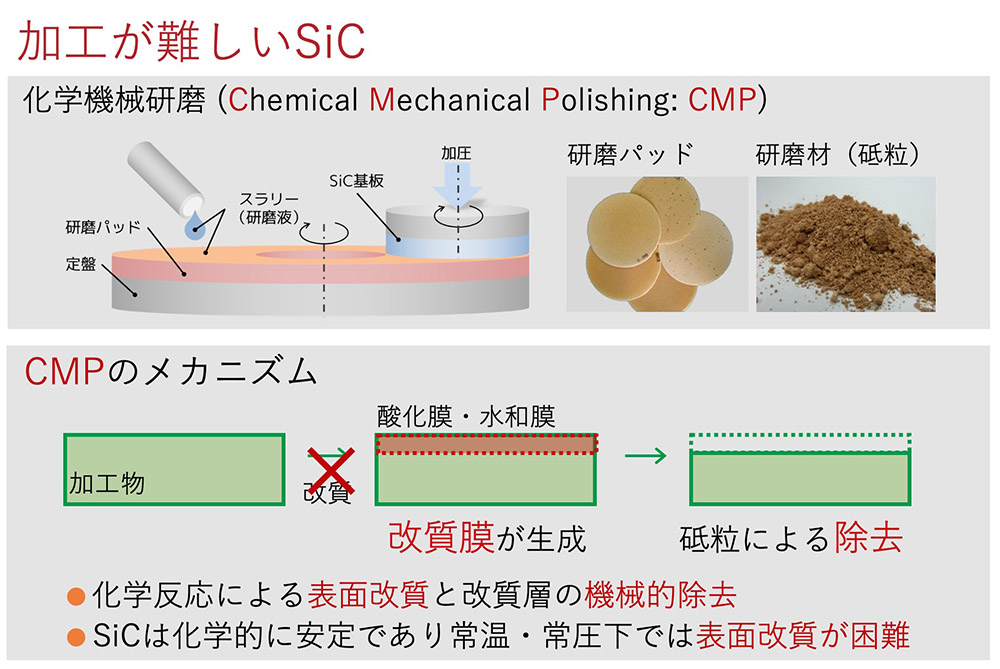
「SiCは非常に硬い材料で、ダイヤモンドに次ぐ硬度を持っているほどです。しかも、化学的に極めて安定しており、熱や薬品に対して高い耐性があります。
現状のパワー半導体の基本素材であるシリコンでは、半導体製造過程で『表面を薬品で溶かしながら削る』ことができました。しかし、SiCの場合は、溶かせる薬品が存在しないので、表面を平滑にする別の技術が必要になります。一部の電車などにはSiCのパワー半導体が既に採用されていますが、従来のものに比べて非常に高価なものになっています」
薬液を使用せず、研磨工程を短縮できる研磨技術を開発
難しいSiCの研磨加工の技術開発が、まさに村田准教授の研究テーマだ。その研究内容の一端を紹介しよう。
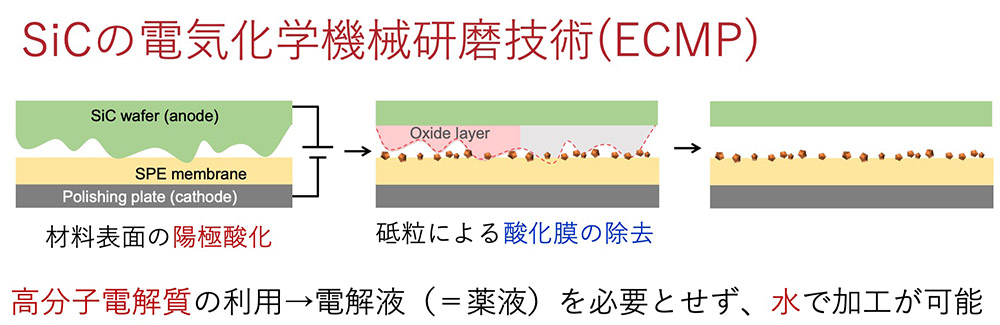
「研究の趣旨を簡単に言えば、『SiCに電気を流して研磨しやすくする』ことです。SiCに電気を流す、つまり電気分解すると、表面が“ふやけた”ような状態になり、少し軟らかくなります。ガラスに近い軟らかさの成分になるので、その状態で研磨するわけです。
SiCを電気分解して研磨する技術自体は、他の研究グループでも開発されていますが、私の研究では、電気分解をするときに、薬品を使わないのが特徴です。固体高分子電解質という物質を活用することで、『薬品を使わず水だけで電気分解できる』ため、環境や製造設備、作業する人の負担軽減が可能です。
また、この新しい研磨技術が実用化されれば、半導体の基板の加工時間を大幅に短縮することも可能になります。従来の技術では、基板の表面を平滑にするのに数時間かかったのが、5分程度にまで短くできるのではないかと考えています」
この「加工時間の短縮」は、生産性の向上に直結するため、研究成果としては非常に大きなインパクトを持つ。SiCを用いたパワー半導体の技術は日本の得意分野であり、自動車や自動車部品のメーカーをはじめ、オールジャパンで取り組んでいるという。
ところで、SiC表面の平滑度は、どれほどなのだろうか。
「基板の表面の『粗さ』として、現在の指標になっているのが0.5nm程度です。0.5nmというのは、およそ原子数個分。原子2~3個分といったところでしょうか」
私たちの生活をいたるところで支えているパワー半導体に、“それ以上平滑にしようがない”ほどの平滑性が求められていることは、驚くばかりだ。
パワー半導体の加工プロセスの改善で、日本の競争力向上へ
未来の私たちの生活にも大きな影響を及ぼす、次世代パワー半導体。村田准教授の研究の延長線上には、どのようなビジョンがあるのだろうか。
「現在の研究開発の目標はSiCを用いた基板の大口径化です。今、研究室で研磨しているSiC基板は直径50mm(2インチ)のものですが、実際の半導体の基板は4インチ(直径100mm)から6インチ(直径150mm)あります。産業に応用するためには、どうしても大口径化が必要ですが、実際にはさまざまな課題があります。
ひとつは、大口径化すると『ムラが出る』という点です。ある部分は加工できているのに、真ん中の部分はなかなか加工されないケースなどが予想されます。これから大型の基板を研磨するテストを重ねて、ムラを生じさせない最適な研磨方法を見つけなければなりません。
また、製造したパワー半導体の『評価』にも課題があります。半導体の難しいところは、完成品を実際に作動させてみないとわからないことが多いという点です。半導体は汚染や不純物を非常に嫌うので、この加工方法で半導体の特性を損なうような要因はないか、基板の表面の状態は保たれているかといったことを評価しなければなりません。
半導体の基板には平滑性だけでなく、表面にダメージがないことも要求されます。評価の作業は私たちの研究室だけではできないので、別の研究グループと連携しながら進める必要があります」
研究の最前線には、言うまでもなくさまざまな課題がある。しかし、こうした課題を解決し、次世代のパワー半導体の加工プロセスが大きく改善される可能性は高いだろう。この技術が実際の製造工程に導入され、SiCパワー半導体が普及するとき、私たちの生活にも変化が訪れているはずだ。そしてそのことは、この分野における日本の競争力拡大にも大きな影響をもたらす。
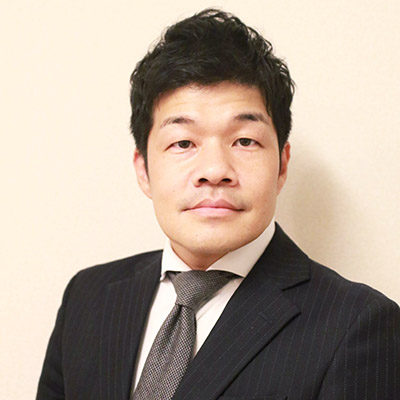
村田順二
大阪大学大学院工学研究科博士課程修了(博士(工学))。立命館大学理工学部助教、近畿大学理工学部講師・准教授を経て、2019年4月から現職。機能性材料の表面創成技術の開発に従事。